We are driving digitalization forward
The digital transformation is well under way in many branches of industry. To enable us to make the most of the opportunities which Industry 4.0 presents to us and our customers, we set up a new organizational unit in 2016 – the Digitalization Center.
A team of sensor, electronics, software, data and cloud specialists are currently driving digitalization forward there. The team’s playing fields are on the one hand digital services for our customers and on the other the transformation of our internal value added. In both cases, the aim is to increase efficiency. Making WITTENSTEIN employees fit for the digital world is another major focus.
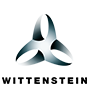
+49 7931 493-0
Our vision
Self-learning products and systems become interconnected through digital awareness.
WITTENSTEIN products know their natural environment and interact independently within it. They communicate, learn, watch and grow with their related products, machines, systems and networks.
Human beings at the center of the factory control the value chain by means of the virtual replica.
The human beings at the center of the factory control the physical value added by means of virtually networked replicas of the value chain formed by suppliers, customers and WITTENSTEIN.

Four agile trains
In order to capitalize on the opportunities of digitalization, the Digitalization Center has defined four strategy fields, referred to as agile trains: Smart Factory, Smart Products & Data Driven Services, Smart Customer Journey and Digital Transformation.
Smart Factory
The central challenge facing industry lies in finding a way to make growing complexity and the increasing trend towards mass customization manageable. This can only happen within a digitally networked manufacturing environment. The Smart Factory train, therefore, addresses an environment in which production machinery and logistics systems are linked to human beings and have the capability to organize themselves. This human centered digitalization focuses on a shared learning process for all employees as a basis for seizing the opportunities of digitalization wisely.
Support for employees on the line
One current project involves the implementation of a CPS (cyber-physical system) to support employees on the line and achieve higher process reliability. This CPS allows order and process-related data on the workpiece to be made available directly at the workplace. A touch screen provides employees with information on necessary materials, process descriptions and additional visual information to simplify assembly (pick-by-light).
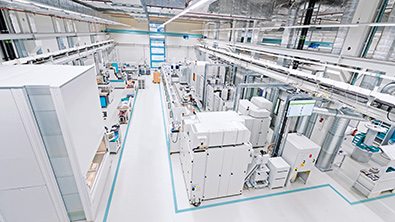
Smart Products & Data Driven Services
If information flows must be made more efficient, and simulation options created, during a product’s planning and development phase, we can offer totally new services to our customers in the use phase. This is precisely what the Smart Products & Data Driven Services train is all about. Cloud capabilities and the Internet of Things mean products can be enhanced with smart services and made interoperable through Industry 4.0 standards.
Digital services for our customers
WITTENSTEIN is presently working on both product and non-product related services. In connection with condition monitoring or predictive maintenance, for example, these services deliver more value added to customers, not only during the use phase. A hysteresis service, say, enables variations in the Galaxie® Drive System’s precision to be detected throughout its lifetime as part of process quality assurance.
The focus when developing and providing such services is on as broad a range of applications as possible – whether in manufacturer or customer-specific systems or in IIoT ecosystems like Siemens MindSphere or Adamos. Our smart services are designed to be operable in predefined ecosystems with a minimum of modifications. We also develop smart sensor and service solutions which do not cause any interruption contours on existing products and can be integrated seamlessly into present and future machine generations.
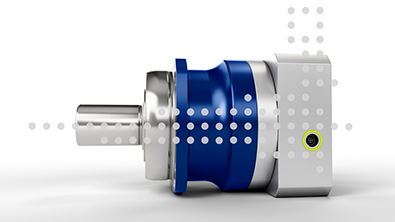
Smart Customer Journey
In the Smart Customer Journey train we develop software that helps our customers find the right product and provides purchase, startup, operating and replacement support. Our cymex® 5, cymex® select and CAD POINT sizing tools are good examples here, along with our WITTENSTEIN Service Portal.
Customized touchpoints along the customer lifecycle
The overall objective is to strengthen customer loyalty by leveraging the new digital opportunities. In the future, elaborate digital touchpoints will accompany the complete customer lifecycle on what we refer to as the so-called Smart Customer Journey. They will contribute significantly to an optimal customer experience at the individual points of contact and help reinforce existing relationships.
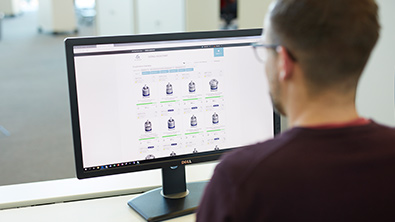
Digital Transformation
Without the Digital Transformation train, all other activities would be impossible. To enable us to become a digital innovation leader, we endorse an agile corporate culture and seek to acquire sustainable skills. This gives us a valuable head start – for instance, when putting ideas into practice or developing new, digital business models.
Human beings are central to our thinking in everything we do: we demonstrate the opportunities that are created by the digital transformation for each employee, encourage them to gain further professional qualifications and provide guidance for dealing with the changes.
Comprehensive networking
The train also puts the emphasis on the maintenance and expansion of partner networks – for example with research institutes, industry associations and universities. Among other things, we collaborate with the German Engineering Federation (VDMA), the Electrical and Electronic Manufacturers’ Association (ZVEI), the Industry 4.0 Platform, the Alliance Industry 4.0 Baden-Württemberg and the Fraunhofer Institute. In the same way, we regard development partnerships with our lead customers as essential for our path into a digital future.
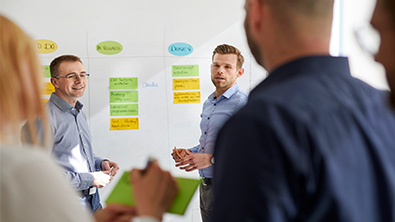
“Digital twin” – an award-winning achievement
The annual “Microsoft Intelligent Manufacturing Award”, jointly organized by Microsoft and management consultants Roland Berger, honors innovative ideas and creative approaches that are driving the transformation to Industry 4.0. Although a very large number of applications were submitted in 2021, WITTENSTEIN was announced as the winner in the “Scale!” category with the implementation of our standardized digital twin, the Asset Administration Shell.
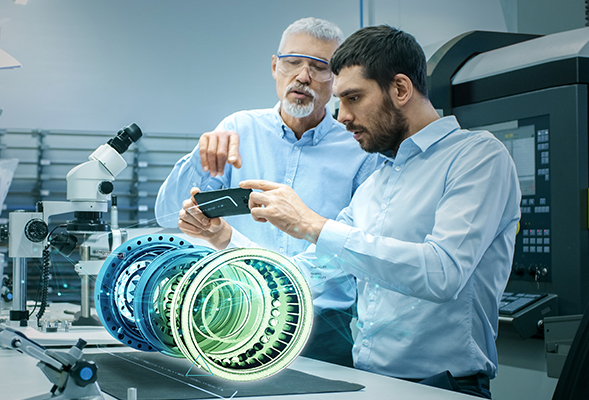
Digitalization can be so easy
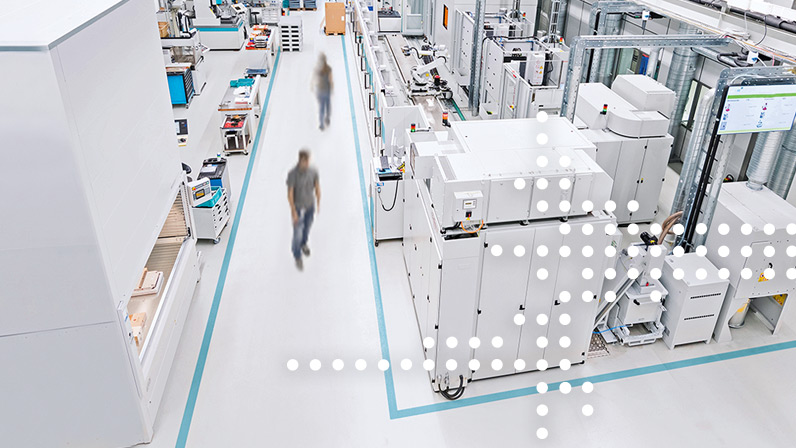
Our video series "Digitalization can be so easy. With solutions by WITTENSTEIN" shows what is already possible today how you can expand your lead in the market with the aid of our products and services. Why not check them out now – and learn more about our smart drive technology and digital services?